Technical Data
- Home
- Technical Data
Air Properties
Components of air Our Planet has air, a mixed gas for which nitrogen and oxygen are main components. However this table refers to air state, and our actual atmosphere includes moisture, dust and contaminants other than items shown in the tableItem/Component | Nitrogen(N2) | Oxygen(O2) | Argon(Ar) | Carbon Dioxide(CO2) | Hydrogen(H2) | Neon(Ne) | Helium(He) | Others |
---|---|---|---|---|---|---|---|---|
Volume(%) | 78.03 | 20.99 | 0.933 | 0.03 | 0.01 | 0.0018 | 0.0005 | – |
Weight | 75.47 | 23.2 | 1.28 | 0.046 | 0.001 | 0.0012 | 0.00007 | – |
Name of Standard | Reference State | Flow Notation |
---|---|---|
ASME Power Test Code | 68℉ 14.7psia RH 36% | S㎥/h Sℓ/min SCRM SCFH |
Compressed Air Institute | 68℉ 14.7psia DRY | |
atural Gas Pipeline Field | 14.7psia – >Suction Temperature | |
Japan Industrial Standards (JIS) | 20℃ 760mmHg RH 65% | |
Korean Industrial Standards ㉿ | 20℃ 760mmHg RH 65% |
- Normal air: air at O°C, 1 aim and 0% relative humidity
- Normal air notation: Nm3 /h,NQ /min, m3 /hfntp), Q /min(ntp),etc
Conversion of measured air
Performance of different compressors is compared by discharged air volume, pressure, etc. Here, the correlation between discharge air volume, normal air volume (Nℓ/ min) and standard free air volume (Iℓ /min) require special attention. Normal air volume is in the unit of Nℓ/min or NTP, and NTP stands for normal temperature & Pressure. This value represents ideal air volume in the academic state, On one hand, the standard air volume is shown as a unit of ℓ /min, This value represents air volume in the industrial standard state for commercial use. The following table shows the two conditions,Item | Normal Air | Standard Air |
---|---|---|
Unit | Nℓ/ min | ℓ/ min |
Reference Temperature | 0℃ | 20℃ |
Absolute Pressure | 760mmHg (1kg/㎠) | 760mmHg (1kg/㎠) |
Relative Humidity | 0% | 65% |
Air Weight | 1.29kg/㎥ | 1.2kg/㎥ |
- Normal air: air at O°C, 1 atm and 0% relative humidity
- Normal air notation: Nm3/h,Nℓ /min, m3/h(ntp), ℓ /min(ntp),etc
- Qt = Qn x (273 + t) / 273 x (760 / pt)
- Qn = Qt x {273 / (273 + t)} x (pt /760)
- Qt :actual discharge air volume( ℓ/min) in suction state
- Qn :actual discharge air volume( ℓ /min)in normal sate
- t :temperature in suctionstate( °c)
- pt :absolute pressure (mmHg) or inhaled gas
Selection of compressor
When selecting an air compressor, a model with appropriate capacity and specification must be selected with consideration on installation area. noise and maintainability. Taking into account calculation error in the computation of capacity, correct on of frequency (load rate), pressure drop in air cleaner and pipe, leakage in pipe joints, and maintenance according to life span of compressor,it is desirable to select a compressor with capacity 1.5 ~ 2 times as large as design capacity.- Air pressure required by consumer
- Necessary air volume (converted to air volume in the atmosphere: free air)
- The frequency of air use (load rate %)
- Cleanliness of air (moisture and oil content)
Air discharge volume in the nozzle
As air discharge volume in the nozzle is maximized when the discharge rate reaches a speed of sound (this is referred to as the critical condition), it is computed by finding flow rate with maximum mass. When a specific heat ratio of air is k=1.4, discharge volume ( ℓ/min) a=rding to maximum mass flow rate is:Mmax = 0.686 x ((,x d2/ 4 x P2 }} I ( √ (R x t2 ) ) x (60 x 1000) / 1.2
d :diameter of nozzle (converted to m)I PO: absolute pressure (converted to Pascal) / R :gas constant of air (conver1ed to Nm/kg°K) / TO:absolute temperature of air (°C+273) When the above equation is rearranged, discharge volume Q (m3/min) is:Q = (273.15 / p ) x ( (πd2/4) x c x Pa) /√ T
d: diameter of the nozzle (converted to mm)/ C : flow constant (1if air)I p: specific weight of air (1.2k9/m3) I TO : absolute temperature of air (°C + 271.15) / Pa:absolute pressure of air (pressure on gauge + 1.0332 kg/cm2) Using the above equation, air injection volume in the nozzle at 20°C can be expressed as a table as follows. [Table of air Injection volume In nozzle]NOZZLE 0m | GAUGE P (kgf/㎠) (m:t:ℓ / min) | |||||||||
---|---|---|---|---|---|---|---|---|---|---|
1.0 | 2.0 | 3.0 | 4.0 | 5.0 | 6.0 | 7.0 | 8.0 | 9.0 | 10.0 | |
0.2 | 0.7 | 1.3 | 1.5 | 1.9 | 2.2 | 2.6 | 2. | 3.4 | 3.6 | 4.0 |
0.4 | 3.0 | 4.4 | 3.9 | 7.3 | 9.2 | 10.2 | 11.7 | 13.1 | 14.6 | 16.0 |
0.6 | 5.4 | 10.0 | 13.2 | 15.4 | 19.7 | 23.0 | 26.2 | 29.9 | 32.8 | 36.0 |
0.8 | 11.8 | 17.6 | 23.4 | 29.2 | 38.0 | 40.3 | 49.6 | 52.4 | 58.3 | 64.1 |
1.0 | 18.4 | 27.8 | 36.4 | 46.7 | 54.9 | 63.8 | 72.9 | 81.9 | 91.0 | 100.1 |
1.3 | 31.2 | 48.5 | 61.8 | 77.1 | 92.5 | 107.8 | 123.3 | 128.5 | 153.8 | 160.3 |
1.5 | 41.3 | 61.8 | 82.3 | 102.7 | 123.1 | 143.8 | 164.8 | 184.9 | 204.8 | 225.2 |
2.0 | 73.8 | 110.1 | 146.3 | 182.6 | 219.0 | 255.2 | 291.5 | 327.8 | 364.1 | 400.4 |
3.0 | 166.0 | 247.8 | 329.3 | 410.9 | 492.6 | 574.2 | 655.9 | 737.5 | 819.1 | 900.8 |
3.4 | 213.2 | 318.1 | 422.9 | 527.8 | 632.7 | 737.5 | 842.4 | 947.3 | 1052.1 | 1137.0 |
3.8 | 266.2 | 397.3 | 528.3 | 639.3 | 790.0 | 821.3 | 1052.3 | 1183.3 | 1314.3 | 1445.3 |
4.0 | 285.1 | 440.2 | 583.4 | 730.5 | 873.7 | 1020.8 | 1165.5 | 1310.5 | 1455.6 | 1601.4 |
4.7 | 407.4 | 607.2 | 808.2 | 1008.6 | 1208.8 | 1408.4 | 1609.7 | 1810.1 | 2010.2 | 2210.9 |
5.0 | 481.4 | 687.9 | 814.6 | 1141.4 | 1366.2 | 1598.0 | 1821.8 | 2046.6 | 2275.4 | 2603.7 |
6.0 | 683.9 | 990.5 | 1317.4 | 1643.7 | 1970.2 | 2296.8 | 2623.4 | 2650.0 | 3276.5 | 3603.1 |
7.0 | 903.7 | 1348.2 | 1792.7 | 2233.2 | 2684.7 | 3126.2 | 3570.7 | 4015.2 | 4459.7 | 4904.2 |
8.0 | 1180.3 | 1760.9 | 2341.6 | 2922.0 | 3502.6 | 4083.2 | 4653.2 | 5244.4 | 5835.0 | 6405.5 |
9.0 | 1493.8 | 2228.6 | 2963.4 | 3693.3 | 4433.0 | 5167.8 | 5908.5 | 6837.4 | 7372.2 | 8107.7 |
Air consumption If using an air cylinder
Since air cylinder discharges compressed air into the atmosphere when the backstroke is performed as force is applied on the piston, air corresponding to cylinder volume x compression ratio is consumed during one-way 1 stroke. Air volume for cylinder operation(1stroke) is:Q ={(π d2 / 4) x S x P} / 1000 (ℓ /min)
d:inner diameter of cylinder (co) / S: cylinder stroke{on)/ P:absolute pressureolcompressed air (gauge pressure + 1.03323kg/cm2 Air volume olreciprocating type inwhich cylinder operation is repeated severaltimes every minute:Q= {{ π d2 / 4) x S x (No. of operations per minute ) x P x 2} / 1000(ℓ /min)
Ex) What is air volume consumed when a cylinder with an inner diameter of 50mm and stroke of 200mm is operated 20 times per minute under air pressure of 61kg/cm2(g)? (single-acting cylinder: returning spring)Q = [π x {(π 52 cm) / 4) x 20cm x 20 times/min x 7.03323 kg/Cm2(a)] ÷ 1000=55ℓ /min *Incase of reciprocating cylinder : 55ℓ /min x 2 = 110ℓ /min
Air consumption by air tools
When computing air volume consumed by air tools that use compressed air as power source, determine the capacity of the compressor based on the table below.Name of Air Tool | Specification | Air Port | Air Consumption(㎥/min) | Appropriate Air Pressure(kg/㎠G) | Note |
---|---|---|---|---|---|
ANGLE GRINDER | 4 inch WHEEL | PT 1/4 | 0.6 | 6.0 – 6.5 | |
7 inch WHEEL | PT 3/8 | 1.5 | 6.0 – 6.5 | ||
Grinder | 11-1/2 inch WHEEL | PT 1/4 | 0.3 | 6.0 – 6.5 | |
SCREW DRIVER | 12 – 4 | PT 1/8 | 0.28 – 0.32 | 6.3 – 6.5 | |
15 – 6 | PT 1/4 | 0.3 – 0.5 | 6.3 – 6.5 | ||
IMPACT WRENCH | 116 | PT 1/4 | 0.5 | 6.3 – 6.5 | |
132 | PT 1/2 | 0.9 | 6.3 – 6.5 | ||
Air Drill | 1¢10 | PT 1/4 | 0.5 – 0.7 | 6.3 – 6.5 | |
라Ratchet Wrench | 112 | PT 1/4 | 0.5 | 6.3 – 6.5 | |
SANDER | 1PAD SIZE 100 x 175 | PT 1/4 | 0.6 | 6.3 – 6.5 | |
Polisher | 1¢205 | PT 1/4 | 0.8 | 6.3 – 6.5 |
Computation of Air Tank Capacity
Generalpiston type compressor requires an air tank to absorb pulsation (vibration of air) and storage of appropriate air, but screw air compressor does not require an air tank because it has almost no pulsation and discharges compressed air using internal compression.
However, when air volume used is temporarily and discontinuously higher (or load in the air quickly fluctuates) than discharge air volume per unit time of compressor, a separate air receiver needs to be installed to promote the efficient operation of compressor.
The equation for computing capacity of air receivers as follows.
V = ( P1 X (01 -02 ) X t } / ( P2 – P3 )
v :capacity of airreceiver (m’)
Pl :inhaled air pressure of compressor (kg/cm2) / P2 :pressure inside air receiver(kg/cm2(a))/ P3 :demanded pressure(kg/cm2(a))/QI :demanded air volume(m2) / Q2:discharge air volume(m2) / t:time during which capacity is temporarily exceeded (MIN)
However, demanded air volume (Q1: m2) indicates air volume required in time during which capacity is temporarily exceeded. The discharge air volume of compressor indicates the value computed by dividing discharge air volume per minute by time tor temporary excess of capacity (when the time of temporary excess is less than 2m)
Ex) What should the capacity of air receiver be when discharge air volume of the compressor is 550ℓ /min and 1,500 ℓ of air with discharge pressure 8.5cm2 is to be discharged in 40 seconds? (Here, pressure inside air receiver is assumed to be the same as discharge pressure of compressor)
Using the equation on above:
V = ( Pl X (Q1 -Q2 ) X t } / ( P2 – P3 )
- Pl : 1.03323 kg/cm2 (a)
- Ql : 1.5 m2 / Q2 :0.55 m2X40sec/60sec=0.37 m2 / P2: :9.53323 kg/cm2(a) / P3 :6.03323kg/cm2 (a) / t :0.67 min(40sec)
V=(l.0332 x (1.5 -0.37 ) x 0.67 } / ( 9.5332 -6.0332 ) = 0.223 ( m2 ) = 223 (m2)= 230ℓ
Air receiver with capacity ol230 ℓ or above is installed.
Installation And Piping
Precautions for installation of the compressor Selection of installation place and foundation for the compressor are greatly restricted by surrounding facilities, and the following matters require special attention. Perform installation work according to the installation guideline provided by the manufacturer of the compressor. 1.Installation place- No rapid temperature change between seasons and day I night As explained earlier, the performance of compressoris extremely sensitive to temperature. When such on air temperature and heal dissipate on in the compressor, especially when attached with air-cooling intercooler, alter cooler and air dryer, the installation place must be maintained at or below 40°C. In places with low-temperature of 0°C below, the high viscosity of lubricant can cause overcurrent during initial start-up. In case of the air-cooling air dryer, condensate can freeze due to lowering evaporation temperature.
- To be installed outdoors to avoid exposure to snow, rain, strong wind, direct sunlight and contamination of inhaled air
- To prevent vibration and impact
- To secure space necessary for transport road,hatch and disassembly inspection
- To have sufficient durability against the weight of machine and operation load
- To have a natural frequency of foundation avoid the range of resonance with excitation force of the machine
- To be careful and perform insulation prevent impact of vibration onbuilding
- Air usage -air usage must be calculated as a momentary load condition. When maximum momentary load condition is not taken into account, lack of pneumatic pressure can lead to malfunctioning of the product.
- Length of pipe- length from air cleaner to final manufacturing facility is computed.
- Allowable pressure drop (pressure loss) – allowable pressure loss occurring is determined based on pipe length. (Pressure loss only in the pure pipe)
- Work pressure of final demand -work pressure at the end of pipe or final place of use is reviewed .
- Conditions of air cleaner use and quant ty of auxiliary materials -since pressure loss occurs as pressure supplied from compressor passes through the air cleaner, primary pipe pressure needs to take this into consideration. It must also include throttle loss from pipe fittings and valves applied to pipe.
Pipe Fittings | Correction Length | Valves | Correction Length | ||
---|---|---|---|---|---|
90℃ Elbow | d=3/8"~ 21/2" d=3"~ 6" d=7"~ 10" | 30times d 40times 50times | Globe Valve | d=1"~ 21/2" d=3"~ 6" d=7"~ 10" | 45times d 60times 75times |
90℃ Band 45℃ Elbow T Fitting + Fitting | R/d = 3 ~ 5 d = 1"~ 3" | 10~20times d 15~20times 40~80times 50times | Butterfly Valve | 100% open 75% open 50% open 25% open | 0times d 10times 100times 900times |
90℃ Angle Valve | 100~120times pipe diameter d |
ΔP=4 x fx { L x p x v2 } x (d x 2 x g } + Correctionlength
ΔP:pressure dropin kg/m2, f:friction coefficent , L:tength of pipe in m, p:density of fluid in kg/m2,v:mean velocity of fluid in m/sec m/sec,d :inner diameter of pipe in m,g:gravitational acceeration – 9.81 m/sec2 [Table for Selection of Pipe Diameter]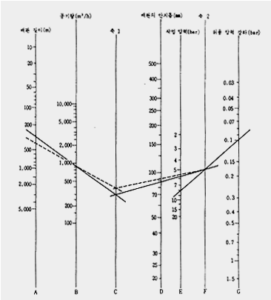
Inner Diameter of Pipe | f | Inner Diameter of Pipe | f | Inner Diameter of Pipe | f | Inner Diameter of Pipe | f |
---|---|---|---|---|---|---|---|
25.4 | 0.01242 | 228.6 | 0.00378 | 431.0 | 0.00327 | 635.0 | 0.00309 |
50.8 | 0.00756 | 254.0 | 0.00367 | 457.2 | 0.00325 | 660.4 | 0.00307 |
76.2 | 0.00594 | 279.4 | 0.00358 | 482.6 | 0.00321 | 685.8 | 0.00306 |
101.6 | 0.00513 | 304.8 | 0.00351 | 508.0 | 0.00319 | 711.2 | 0.00304 |
127.0 | 0.00464 | 330.2 | 0.00345 | 533.1 | 0.00316 | 736.6 | 000304 |
152.4 | 0.00432 | 355.6 | 0.00340 | 558.8 | 0.00314 | 762.0 | 0.00302 |
177.8 | 0.00409 | 381.0 | 0.00335 | 584.2 | 0.00312 | ||
203.2 | 0.00392 | 406.4 | 0.00331 | 609.6 | 0.00310 |
Fittings | n | Valves | n | ||
---|---|---|---|---|---|
90℃ Elbow | d=3/8"~ 21/2" d=3"~ 6" d=7"~ 10" | 30 40 50 | Globe Valve | d=3/8"~ 21/2" d=3"~ 6" d=7"~ 10" | 45 60 75 |
Standard90℃ Band Elbow 45℃ Elbow T Fitting +-shaped Fitting | R/d = 3 ~ 5 d = 1"~ 3" d = 1"~ 3" | 10~20 15~20 15~20 40~80 50 | Butterfly Valve | Fully open 3/4open 1/2open 1/4open | 0 10 100 900 |
90℃ Angle Valve | 100~120 |
Operation And Lubrication Management
Trial Operation
Tiral operator in compressor is generaly performed by manufactor or installer according to the following seequence:
1. Before Operation
Operation Sequence | Precaution |
---|---|
Check connection of power and grounding, and make sure that voltage is within the regulated value. | Prevent malfunctioning by connecting power grounding to the ground surface. |
Supply lubricant until it reaches upper limit of oil level gauge. | When lubricant becomes insufficient after starting the device as it flows into oil cooler, stop the compressor and check that pressure reaches 0kgf/㎠(G) before resupplying oil. |
Check tension on V-belt (in case of motor V-belt type). | Check suspension of power. |
Supply cooling water to cooler (in case of water-cooling type). | |
Stop (power) lamp is turned on when power is supplied. | In case of reverse phase, reverse phase relay is operated to turn “reverse power phase” lamp on. The compressor cannot be operated. |
2.Operation
Operation Sequence | Precaution |
---|---|
Completely open the discharge valve and press start button. | Pressure suddenly rises when the machine is started with the valve closed. |
During no-load operation, slowly close the discharge valve at discharge pressure of 4kg/㎠(G). | If discharge pressure is higher or lower than 4kg/㎠(g) when the discharge valve is completely open, adjust holding pressure valve. |
Check vibration, noise and oil leak. |
3.During Operation
Operation Sequence | Precaution |
---|---|
Allow discharge pressure to reach discharge pressure in the specification. Check the meter values under full load operation. | When no-load operation starts, pressure inside oil separation tank is discharged to reduce discharge pressure (inside unit). No-load operation is carried out while maintaining discharge pressure of 1~2.5kg/㎠(g). |
Pull the safety valve ring to check its operation. (Open the inspection door on the front of package or inspection hole on the side) | Setting pressure of safety valve is as follows. For 7.0kg/㎠(g) specification: 8.5kg/㎠(g) For 8.5kg/㎠(g) specification: 9.5kg/㎠(g) For 9.5kg/㎠(g) specification: 9.9kg/㎠(g) |
4.Stop
Operation Sequence | Precaution |
---|---|
Press stop button. | As soon as the motor stops, auto air discharge valve discharges compressed air from oil separation tank to the atmosphere, which generates a sound for about 30 seconds. |
Make sure that pressure gauge indicates 0kg/cm2 (g) after the machine comes to a stop. |
Routine Operation
1) Operation Sequence
Before operation
Open the condensate drain valve at the bottom of front side of the cabinet to drain condensate out of oil separation tank. After draining condensate, inspect oil level gauge to make sure that lubricant is within the gauge limit. Check whether power lamp is turned on. Supply cooling water to the cooler. (For water-cooling type)
Operation
Completely open the discharge valve and press the start button to start the compressor. Slowly close the discharge valve to increase pressure.
During operation
Inspect meter values under full load state. Check for abnormalities in meter lamps. (Record meter values onDaily InspectionRecord) Pull the safety valve ring to confirm proper operation(checked at every 500 hours).
Stop
Press the stop button. Make sure that pressure gauge indicates Okgf/cm2 (g) after stopping. Block cooling water and discharge cooling water inside the cooler. (For water-cooling type)
2. Precautions for Winter Operation
When operating the compressor under low atmospheric temperature (surrounding temperature), the compressor may not rotate smoothly or automatically stop as soon as it starts. (Overcurrent display: EOCR) This is caused by increased viscosity from a low temperature of lubricant. In this case, increase the temperature of lubricant by repeating the operation of the compressor 2 ~3 times.
Lubricant management
Functions of oil include lubrication, cooling, sealing, rust prevention and stress dispersion. When an inappropriate lubricant is used, bearing fixation, damaging of the valve from the generation of hard carbon, and leakage from each sealing part (between rotor and casing, piston, piston ring and cylinder part) can result in reduced performance and reduced life span. On one hand in refrigerant compressor, the inappropriate lubricant can prevent ideal separation from the refrigerant. reduced stability . and clogging of capillary tube or expansion valve. Functions are as follows.
- Lubrication: forms an oil film on the friction surface to reduce friction between metals
- Cooling: cools compression heat during air compression to prevent overheating
- Sealing: prevents leaking of pressure
- Rust prevent on: prevents oxidization by preventing contact with oxygen, water and corrosive gas using oil film formed on the metal surface
- Stress dispersion: load on the friction surface is evenly dispersed to reduce impact and wear
Type of lubrication is divided into complete lubrication and boundary lubrication depending on the lubrication state. Complete lubrication (fluid lubrication)is the most ideal case in which two adjacent objects are completely separated by oil. Boundary lubrication(thin film lubrication) is the case in which two moving objects show partial friction as they contact each other through thin oil film. Most objects are operated in boundary lubrication state. Another type of lubrication is called extreme pressure lubrication. The friction surface is sometimes destroyed by excessive load or high temperature of the friction surface, and extreme pressure lubrication forms an extreme pressure film using an additive to prevent this destruction phenomenon.
In general, lubricants exhibit optimal performance at 50-60°C, and oil film becomes thin or is decomposed at or above 65C. (Actual decomposition temperature differs for each lubricant, but it is mostly around 120C. Since this refers to the local temperature of the lubricated part, general upper Jim of tank temperature should be set to 105C.)
Management of lubricant is an item of inspection before starting of the compressor. 1/4 position of oil level gauge is considered as the lower limit. When a new compressor is to be used, the lubricant must be completely drained and replaced after 500~600 hours of use. When the lubricant is to be continuously used, lubricant recommended in the compressor manual must be used for 2,0003.000 hours. If it is difficult to purchase the recommended lubricant, the same type of base oil with same viscosity must be selected (be careful as there are many different types of commercial base oil including alkylbenzene, synthetic lubricant, paraffin, naphthene, silicon, olefin, ester, polyester, and poly alpha glycol).
Dehumidification
Dehumidification comprehensively refers to the work of removing moisture in the air and various gases and converting air or gas to dry state. General types of dehumidification include cooling dehumidification and compressed dehumidification, and chemical dehumidification.
Cooling dehumidification
Cooling dehumidification is a method in which air is cooled below dew point to condense moisture in the air into water and reheated alter removing condensed moisture to obtain air with low humidity. Refrigerant, cooling water and brain of the refrigerator are used as cooling sources of air, and it has the following characteristics. [Characteristics of cooling dehumidification]
- When the surface temperature of cooling coil drops below O’C, condensed moisture freezes on the surface of the coil and reduces cooling efficiency, making it difficult to obtain constant humidity.
- Cooling efficiency is reduced when relative humidity is high, such as during the rainy season.
- Limitation of this dehumidification method in general use is dew point temperature of O°C or above.
- Size of the facility is increased with power consumption, resulting in increased cost of operation.
Compressed Dehumidification
Compressed dehumidification is a method in which air is compressed to reduce its volume and cooled. Moisture in the air is condensed into moisture. Air is reheated alter removing moisture to obtain air with low humidity. it has the following characteristics. [Characteristics of compressed dehumidification]
- This method is applied for dehumidification with small wind and low humidity.
- This method requires high power cost for compression,
- This method is applied when high pressure dehumidified air is needed tor instrumentation, etc.
Compressed dehumidification method uses cooling cycle facilities using compressed air to cool air down to pressure dew point of O°C.
Chemical Dehumidification
Chemical dehumidification is divided into absorbent batch type and absorbent liquid type, and each has the following characteristics.
Absorbent batch type uses two or more towers by filling solid adsorbent (silica gel, active alumina, zeolite, etc.)into the cylindrical tower. When there are two lowers, one top is used to absorb dehumidified air. Regeneration is performed by switching to the other tower alter certain time. Dehumidification is carried out by capillary tube acting on the surface of absorbent.
[Characteristics of chemical dehumidification – absorption bath type]
- Dehumidified air with low dew point can be obtained depending on the solid absorbent selected.
- As dehumidification and regeneration are switched at a prescribed timing, dehumidified air cannot be obtained continuously.
- Regular replacement of absorbent is required.
The device shows a large pressure loss. - Regeneration temperature is high.
Absorbent liquid type uses lithium chloride solution as absorbent and consists of dehumidification part and regeneration part. When absorption solution sprayed inside dehumidification part contacts air to be dehumidified, moisture in the air is absorbed by solution due to the difference in partial pressure between the absorbent solution and water vapour in the air. Condensation heat and absorption heal occurring from absorption are removed by the cooling coil. The solution that absorbed moisture is returned to the regeneration part using liquid circulation pump contact air heated by heat coil. Here, moisture in absorbent solution is evaporated into the atmosphere. The concentrated solution is sent back to the dehumidification part alter regenerate on for circulation.
[Characteristics of chemical dehumidification – absorbent liquid type]
- As dehumidification and regenerate on are continuously carried out, dehumidified air can be constantly obtained.
- Carry-over (the phenomenon in which solution is discharged with wet air being discharged from regeneration partly atmosphere) of the solution must be prevented.
- As deposition of lithium chloride can occur depending on concentration and temperature of the solution, the concentration of solution needs to be managed
- Regular supplementation and replacement of solution are required.
Compressor Test Standards
Test methods for air compressor and refrigerant compressor shall follow methods regulated in KS. Testing method and conditions for each compressor regulated in KS are in the following table.
[ Test standards for compressor in KS ]
Name of Standard | Standard No. | Test Conditions |
---|---|---|
Testing and inspection methods for volumetric compressor | KSB 6351 | Repetitive and rotary compressor with pressure ratio of 2 or higher suction temperature 20°C, suction pressure 101.3kPa, relative humidity 65% |
Testing and inspection methods for turbo type blower and compressor | KSB 6350 | Turbo type ventilator and compressor with pressure ratio of 1 or higher suction temperature, suction pressure and relative humidity same as above |